Inglis Dryer Repair
Certified & Experienced Inglis Dryer Repair in Scarborough and Surrounding Areas
How to Repair A Inglis Dryer?
If you have been experiencing a problem with your Inglis dryer, you are not alone. Most of us have encountered this problem at some point. If your dryer is still working, but not drying properly, you should check the thermostat first. You can also check for a clogged air passage or broken multi-rib belt. A blown thermal fuse is another potential cause of your trouble. If none of these issues are the cause of your trouble, you can try the following methods to repair your dryer in scarborough.
Symptoms of a faulty thermostat
The first thing you should do if you suspect that your Inglis dryer has a faulty thermostat is to unplug the appliance and check the wiring. The wiring leads from the thermostat to the heating element. If the wiring leads are disconnected or if you feel that the thermostat is not working properly, you can connect a multimeter to each terminal. If the wire leads are still connected, then the thermostat is working correctly. Otherwise, you should replace it.
The switch is located near the door and is critical to the operation of the dryer. If this switch is malfunctioning, the door cannot close properly. It should be a white prong that operates like a spring-loaded button. If the switch is stuck, the switch is probably faulty. Thermal fuses are used in most dryers to protect them from overheating. The thermal fuses are located near the blower, heating element, and burner housing.
Checking for a clogged air passage
One of the most common causes of a humming noise in your Inglis dryer may be a clogged air passage. A clogged air passage can cause undue strain on the motor. Another cause is a worn fan belt. You can treat the fan belt by dressing it, which you can buy from home centers, automotive stores, or hardware stores. Some noise is normal.
Another cause of a clogged air passage is lint buildup. This lint clogs the exhaust vent, which can be located through an exterior wall or basement window. To clean the air passage, remove the back service panel and remove any lint that is stuck inside. You can then reassemble the parts of the dryer. If you notice any lint, you can also inspect the motor shaft.
Checking for a broken multi-rib belt
One of the most common problems with a washer or dryer is a broken multi-rib belt. It’s an OEM part that attaches to the motor, drum and idler pulley. It can wear out or become frayed and inflexible. In addition, you may notice that the drum is not turning, the motor runs all the time but the dryer isn’t producing heat, you might notice strange noises while running, or you may experience a burning smell in the dryer’s interior. If you’re experiencing any of these symptoms, the multi-rib belt is likely broken. To check for broken belts, simply lift the dryer’s drum and look for a belt tensioner.
The old belt is usually threaded around the idler pulley or motor drive shaft. If you’re unsure, you can sketch the installation diagram to help you identify the right pulley for your machine. You can also cut off the worn belt from the drum as a pattern. The drum may also be jammed with a frayed or broken multi-rib belt.
Checking for a blown thermal fuse
Checking for a blown thermal fuse in an Inglis dryer is simple – a blown fuse is a sign that the fuse is tripped. You can test the fuse by placing a digital multimeter or ohmmeter on the affected thermal fuse. Check if the needle moves to 0 or stays the same. If it changes, the thermal fuse is tripped.
To check for a blown thermal fuse, first make sure the electrical outlet is turned off. During this time, you can perform troubleshooting steps. Look for the thermal fuse on your dryer’s exhaust vent. Different models have different locations for thermal fuses. You can check the owners manual or search online to find the location. Make sure you have the fuse located before attempting to fix the dryer.
Checking for a clogged timer
Is your Inglis dryer tripping on you? If so, check the thermal fuse. This is the part that prevents the dryer from heating up to the maximum temperature. If it is shorted, replace it. Alternatively, you can open the door and use an ohmmeter to check the internal components. The thermal fuse is easily accessible near the exhaust hose.
The timer is a small electric motor that operates a series of cams and gears. When the timer is faulty, the dryer will spin without producing heat, and the cycle will not advance. In the meantime, the heat will continue to accumulate. This is an indication that the timer motor is defective. If you can’t diagnose the issue yourself, you can contact a service technician.
Checking for a faulty electronic control board
Checking for a faulty electronic control panel is one of the most common repair procedures for an Inglis dryer. Most dryers have a control panel that is located on the back of the appliance, usually above the power cord. Disconnect the dryer from the power source and remove the access panel. Visually inspect the terminals for signs of burning or overheating. If any of these components appear damaged, it is time to replace the electronic control board.
If the dryer does not shut off automatically, a faulty switch can cause this problem. The door switch pushes against a thermal fuse located on the blower housing. The thermal fuse will have a continuous electrical path when it is working properly, but will break when it is overheated. To test the switch, use a volt-ohm-millimeter set to RX1 scale. The switch should read zero when tested correctly. If the switch is faulty, replace it with a new one.
Happy Customers

“Sam was able to get to my house the same day I called and checked out my dryer. He was extremely professional and had all the parts required for the repair on him. I would definitely recommend his services to anyone and will be coming to Scarborough appliance repair if i need anymore repairs.”
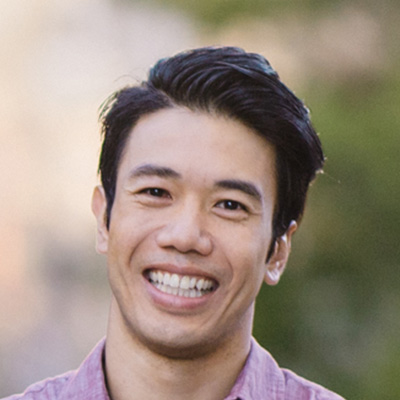
Jimmy Cho

“My fridge wasn’t cooling and Sam was able to get me an appointment on the same day to diagnose the issue. He found out quickly that there was a drain and defrost problem and surprisingly came prepared with the parts required to complete the repair and got it done that same afternoon. Thanks again sam!”
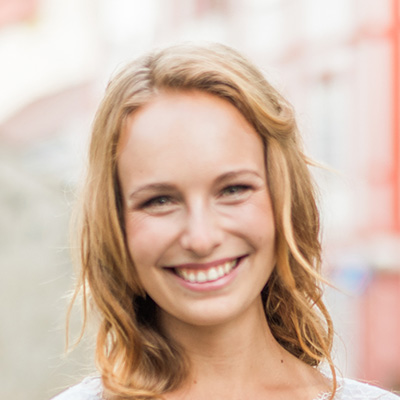